Safety products maker strengthens workers’ skillsets with co-op workforce grant
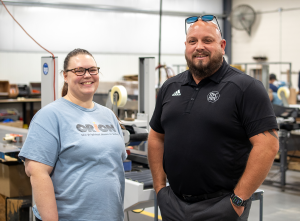
Chelsey Kamleiter, human resources generalist at Orion Safety Products, and Mike Barron, director of marketing and member services for Miami-Cass REMC. Barron worked with Kamleiter on the Workforce Automation Grant that the business received from Miami-Cass REMC and Wabash Valley Power Alliance.
Human resources professional Chelsey Kamleiter’s eyes lit up as she learned of a way to train her company’s employees that make emergency flares – thanks to the organization’s local electric co-op.
Orion Safety Products, an emergency flare and safety product manufacturer based in Peru, Ind., received a Workforce Automation Grant for more than $5,000 from Miami-Cass REMC, its local electric cooperative, and Wabash Valley Power Alliance, the wholesale power provider for Miami-Cass. Orion Safety Products utilized the grant for several kinds of employee training, including leadership development. The company also will have two trainers from the local Ivy Tech Community College branch provide required hazardous materials training for the chemicals needed to create flares and other products.
“I saw an opportunity that we didn’t have prior and maybe do what we couldn’t before, which was more than just annual training,” said Kamleiter, the human resources generalist for Orion Safety Products. “This just provides us many improved training options.”
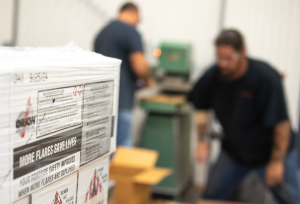
Orion Safety Products employees pack boxes at the company’s warehouse in Peru, Ind. The business received a Workforce Automation Grant for more than $5,000 from Miami-Cass REMC and Wabash Valley Power Alliance for several types of employee training.
She learned about the grant during an economic development meeting that featured a presentation by Mike Barron, director of marketing and member services for Miami-Cass. The grant is open to all businesses served by electric distribution co-ops that are members of Wabash Valley Power.
“This allows a company to be able to do these trainings now because the grant can take that stress off that company needing to budget for it, especially during times of economic uncertainty,” Barron said. “Now instead of possibly considering a budget cut for training, you’re having that training and can still conduct business and grow and retain those employees.”
Orion Safety Products is the only flare manufacturer in the nation, Kamleiter said. Because the company features unique equipment, it can be difficult to find trainers to provide employee education. The grant paid for more than a dozen employees to receive training; the business has 87 employees that work at its Indiana site.
The hazardous materials training is incredibly important, as the company receives multiple chemicals to create flares and other products. The Ivy Tech trainers provide detailed site-specific training that is more thorough than online courses, Kamleiter said.
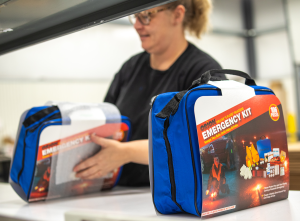
An Orion Safety Products employee packs emergency kits in the company’s warehouse. The business received the Workforce Automation Grant to train employees in several areas, including hazardous materials training.
“We want to make sure that our employees know everything they possibly can,” she added. “Safety is incredibly important. It’s very much at the top of the owners’ list.”
Barron supported Kamleiter through the application process, which consists of a few questions and documentation of the training. She talked with Barron and completed the application, then submitted the training receipts for reimbursement.
“I tried to explain to upper management that this was the process,” Kamleiter said. “They are just used to having things have so many steps involved, they were surprised because it was so simple.”
The grant can be used for a variety of kinds of training for new or current employees to learn new software or equipment, as well as required specific job training. Wabash Valley Power works with its member co-ops and participating businesses to ensure that the grant can be responsive to the company’s needs.

An Orion Safety Products employee packs emergency kits at the company’s warehouse in Peru, Ind. The company is the only flare manufacturer in the United States.
“We want this grant to be responsive to companies’ needs to ensure that they can benefit,” said Zyan Miller, economic development relations specialist for WVPA. “The business world is rapidly evolving, and that can create new opportunities and challenges for companies. We and our member co-ops want to support businesses to make sure that they can continue to invest in our communities.”
Many businesses want to find ways to upskill and retain their workforce, which can be a challenge in rural areas, Barron said. He noted that continuous training can show employees how the business is investing in keeping them.
“I believe that when you feel like a company is investing in you,” Barron said, “you tend to want to stay with that company.”